deadkitty
Well-known member
Hello All-
I've been lurking these forums for quite awhile, and now I finally own a jon boat. Went out and got some good deals on the boat and ski. It's a Sea King 12 footer, 32" wide; the ski is a 94 kawasaki xi with a ported 650 engine. My brother and I are taking on quite a project this winter in hopes to have her seaworthy by spring. We are essentially combining a couple builds we've seen on here and across the web. The first thing we want to do is widen it to around 50" to make her nice and stable. From there we plan on dropping the ski motor into to it :lol: then decking it out and adding all the creature comforts and pretties. We know there's the possibility of complete and utter failure. But we say "go big or go home", lol.
Anyway, should be fun. If it fails it will be a good experience to learn from.
Any words of wisdom as we embark on this journey?
do's and don'ts? (and no don't do it is not an option... we are goin for it!) :LOL2:
I'm sure we will have questions along the way and we'll be sure to ask.
sea king 12'
kawasaki xi
motorguide stealth 300
I've been lurking these forums for quite awhile, and now I finally own a jon boat. Went out and got some good deals on the boat and ski. It's a Sea King 12 footer, 32" wide; the ski is a 94 kawasaki xi with a ported 650 engine. My brother and I are taking on quite a project this winter in hopes to have her seaworthy by spring. We are essentially combining a couple builds we've seen on here and across the web. The first thing we want to do is widen it to around 50" to make her nice and stable. From there we plan on dropping the ski motor into to it :lol: then decking it out and adding all the creature comforts and pretties. We know there's the possibility of complete and utter failure. But we say "go big or go home", lol.
Anyway, should be fun. If it fails it will be a good experience to learn from.
Any words of wisdom as we embark on this journey?
do's and don'ts? (and no don't do it is not an option... we are goin for it!) :LOL2:
I'm sure we will have questions along the way and we'll be sure to ask.
sea king 12'

kawasaki xi
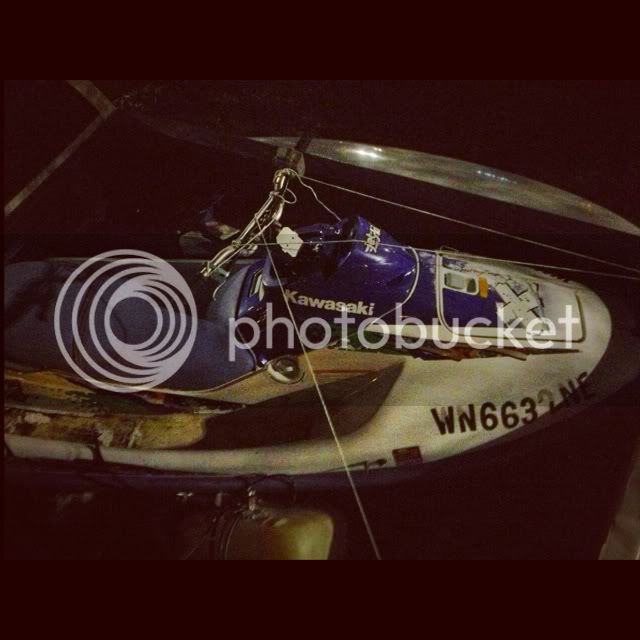
motorguide stealth 300
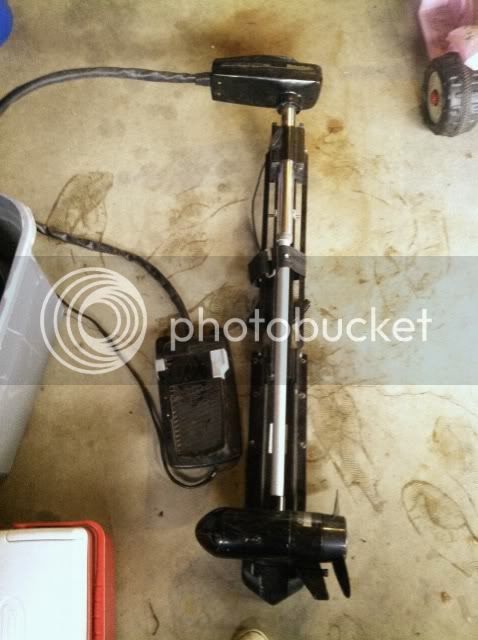
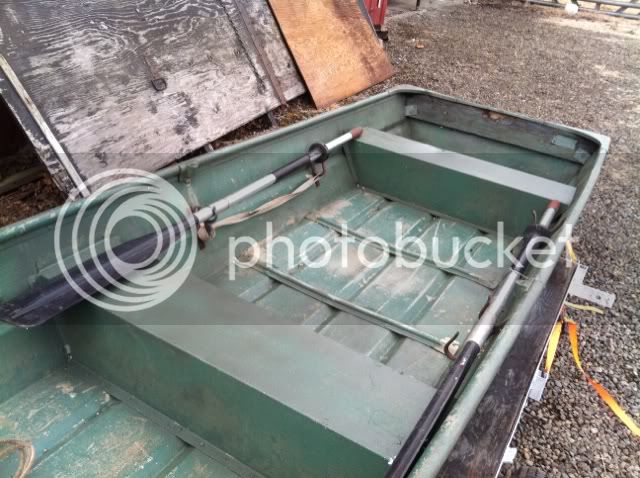
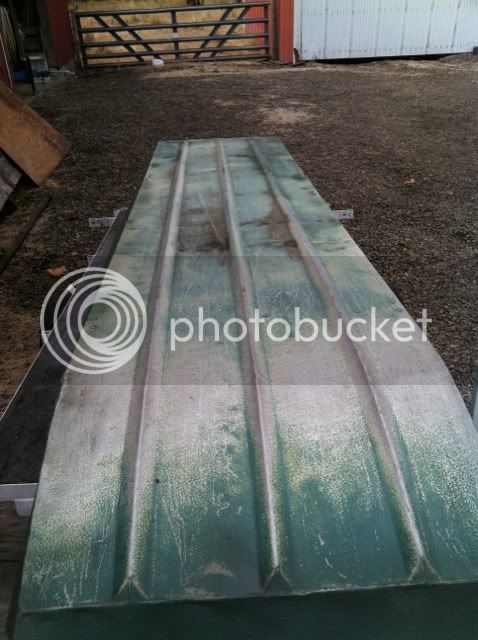
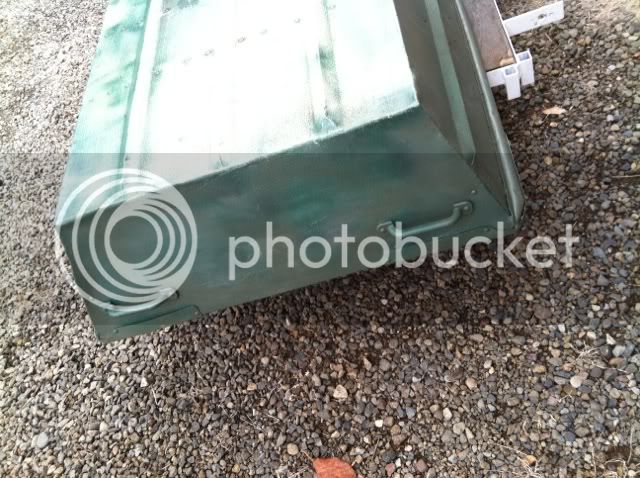