Timbo89
Well-known member
Here is the plan
My trailer is going to be in the area of 17' in total from end to ball. Im going to be making it all out of mild steel 2x3@1/8" thick and the tounge 3x3 @3/16 thick. My tin is a sea nymph 14r at 13'7" and 47" bottom 59 or 57" at the widest point on top. I wanted to be able to put steps around the fenders and put a plastic type of board on the bottom for easy loading. Im also going to put bunk boards for loading it back straight.
Does anyone have any ideas as to what else i sould do. This is the first trailer im going to be making but not the first full fab job ive done. I have a lincoln 175 thats awesome and 72/25 mix.
First boat ive owned too.
I will be starting to get it all layed out and tacked up wednesday. Im off that day so will have time to work on it. This will be coated with primer and semi gloss black paint. I have the lights winch and jack of the old trailer and will be using the axle since it is brand new. I will extend the axle that i have already and be replacing the springs
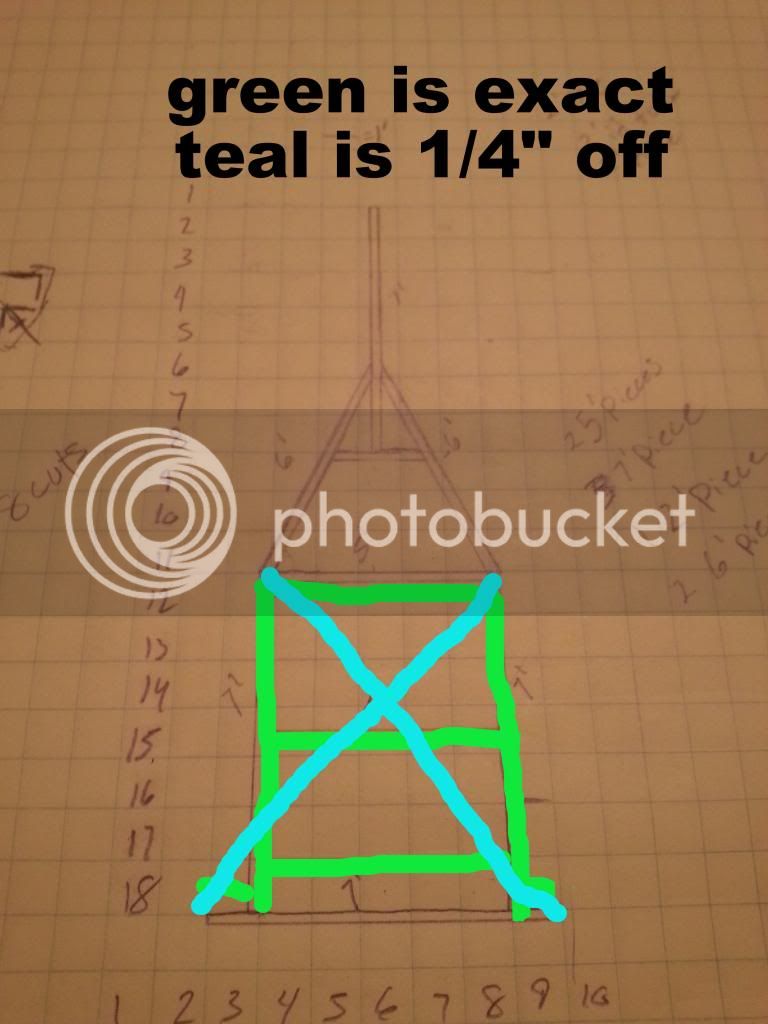
My trailer is going to be in the area of 17' in total from end to ball. Im going to be making it all out of mild steel 2x3@1/8" thick and the tounge 3x3 @3/16 thick. My tin is a sea nymph 14r at 13'7" and 47" bottom 59 or 57" at the widest point on top. I wanted to be able to put steps around the fenders and put a plastic type of board on the bottom for easy loading. Im also going to put bunk boards for loading it back straight.
Does anyone have any ideas as to what else i sould do. This is the first trailer im going to be making but not the first full fab job ive done. I have a lincoln 175 thats awesome and 72/25 mix.
First boat ive owned too.
I will be starting to get it all layed out and tacked up wednesday. Im off that day so will have time to work on it. This will be coated with primer and semi gloss black paint. I have the lights winch and jack of the old trailer and will be using the axle since it is brand new. I will extend the axle that i have already and be replacing the springs