Cheeseball
Well-known member
Well... it's been hard finding time for the boat lately. But, between organizing a kids Halloween party at work (125+ kids), and my 5 mo. old son coming down with a 104 temperature for half a week I found some time for progress.
Most of the steel hardware has been removed. Still working on that. Plus, I managed to remove the old transom.
The bottom edge is pretty rotten. I poked it with a key and could nearly push it all the way through. Here's the stern with the transom board removed.
Here's a hole through the hull where the previous owner had installed a pick up truck bed tie down. (just behind the seat) Since it is in the back of the boat I plan to widen this hole to install the bilge pump discharge. I don't have a drill bit wide enough. Does anybody have a good idea on how I can widen this, or should I just go get the bit?
And now, the part that has me all excited and chomping at the bit to get out on the water! I picked up this 2004 15hp 4stroke with electric start last night. Paid $1,250 for it. The previous owner said it's hardly been used and I believe him. I took the cowl off and the insides are in mint condition. He seemed like a standup guy and his property was kept up immaculately so I figured he's honest and obsessive about keeping things in good condition. I've been looking for a motor like this for quite some time and the new one's range from $2,800 - 2,500. So I figure I got a fair deal.
It also came with a gas tank (full of gas), a prop guard and one of those whale tail thingys. What is the purpose of those? Should I keep it or ditch it?
Well that's all for now...
Most of the steel hardware has been removed. Still working on that. Plus, I managed to remove the old transom.

The bottom edge is pretty rotten. I poked it with a key and could nearly push it all the way through. Here's the stern with the transom board removed.

Here's a hole through the hull where the previous owner had installed a pick up truck bed tie down. (just behind the seat) Since it is in the back of the boat I plan to widen this hole to install the bilge pump discharge. I don't have a drill bit wide enough. Does anybody have a good idea on how I can widen this, or should I just go get the bit?

And now, the part that has me all excited and chomping at the bit to get out on the water! I picked up this 2004 15hp 4stroke with electric start last night. Paid $1,250 for it. The previous owner said it's hardly been used and I believe him. I took the cowl off and the insides are in mint condition. He seemed like a standup guy and his property was kept up immaculately so I figured he's honest and obsessive about keeping things in good condition. I've been looking for a motor like this for quite some time and the new one's range from $2,800 - 2,500. So I figure I got a fair deal.
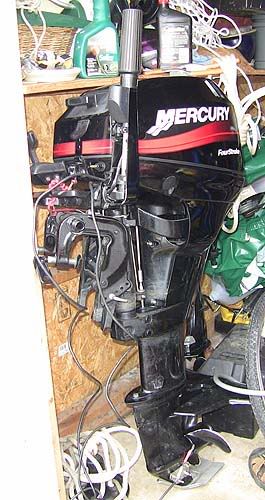
It also came with a gas tank (full of gas), a prop guard and one of those whale tail thingys. What is the purpose of those? Should I keep it or ditch it?

Well that's all for now...