My next order of business in my build is to get the floor and front deck framed out and my aluminum sheet cut. What have you guys done to template out the floor? I have a bunch of cardboard I've been collecting from work that I plan to use to template out my floor this coming weekend. Would this be a better approach than say measuring my dimensions and cutting my aluminum based off of that? My floor will be one large rectangular piece extending the entire width of the boat. But I need to cut my aluminum so it fits around the ribs that extend up the gunwale. This is why I'm thinking a template would be the best way to figure out my dimensions.
Here is what I'm working with.
My floor will extend all the way to the farthest rib towards the bow in this picture (the one that doesn't extend up the gunwale). From that rib fore I'll be adding a small extension to my bow deck.
My floor will butt up against the rear bench. The rib right before the rear bench sits about 1-2" in front of the bench. I'm thinking of cutting a piece of foam board to fit in between the rib and the bench to prevent my aluminum from creasing/bending. Would like to put a piece of angle in there, but there isn't enough room to use a rivet tool. Is foam the best way to provde support in that small area?
Here is what I'm working with.
My floor will extend all the way to the farthest rib towards the bow in this picture (the one that doesn't extend up the gunwale). From that rib fore I'll be adding a small extension to my bow deck.
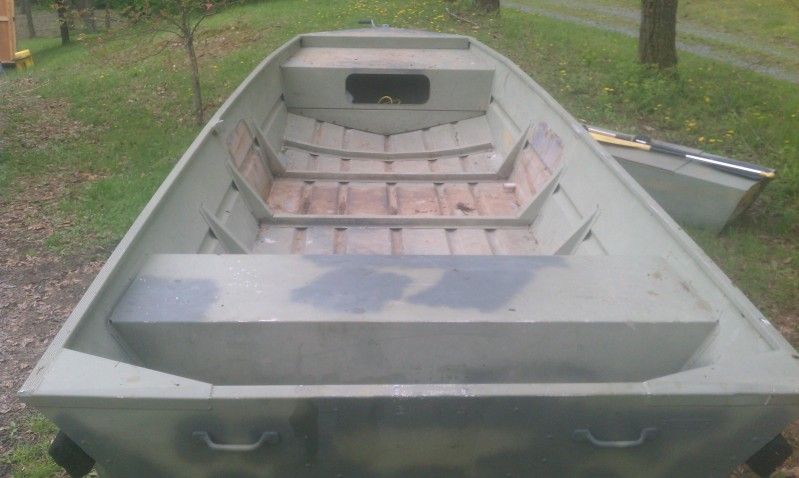
My floor will butt up against the rear bench. The rib right before the rear bench sits about 1-2" in front of the bench. I'm thinking of cutting a piece of foam board to fit in between the rib and the bench to prevent my aluminum from creasing/bending. Would like to put a piece of angle in there, but there isn't enough room to use a rivet tool. Is foam the best way to provde support in that small area?
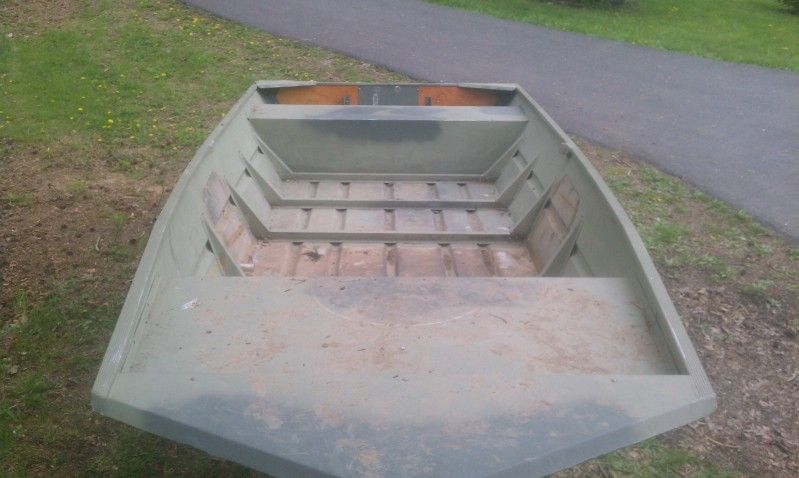